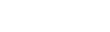
皆さんこんにちは。
カットウェルの山崎です。
今回は世間で、また弊社社内でも、言われている生産性の向上について書きます。
(今回は写真ありません。)
生産性向上の一環として「複合機の稼働率をあげよう」と社内では上司から言われています。
稼働率はその時々の製品により、左右されます。(段取りに時間がかかるが、加工は短時間で済む製品や材料供給回数が多い製品が続くと稼働率は落ちます。)
私としては稼働率アップありきではなく、加工品の手離れの良さ(次工程へ早く加工済み品をわたすこと)が生産性向上につながると考えています。
生産性の向上を考えた時、
①加工にかかる間接工数を今より減らす。
②加工にかかる直接工数を今より減らす。
③直接・間接工数を減らしたうえで同じ内容の受注を増やすことが出来れば改善前より加工できる量が増えるので収益を上げる見込みができる。
※極端な言い方をすれば、工数を1/2に減らし、尚且つ受注量を2倍に増やすことが出来れば、収益も2倍にすることができる。
③部分は極端ではありますが、①、②は実践すべきと考えています。
私が担当している複合機に当てはめてみると…。
①を行う場合、加工以外の工数を減らす。(金型等段取り、移動(材料運搬)など)
②を行う場合、加工時間そのものを減らす。
複合機ではタレットパンチ加工+レーザー加工の組み合わせ、あるいはそのどちらか一方のみの加工を行う。
②-a.タレットパンチ加工に関わる工数を減らす。
②-b.レーザー加工に関わる工数を減らす。
私が加工状況を都度確認しながら、今まで実施した改善内容は以下の通り。
間接工数削減において、実施した改善。
①.金型その1:複合機担当になった当時、複合機用金型置き場に規則性がなかった(作業者のみが置き場所を把握する状態だった)ため、形状ごと、サイズごと、使用頻度を考慮・分別し、置き場所を確保した。
探す時間の減少。
金型その2:セットプレス(パンチ加工を単発で行う機械)用と複合機用金型が共用になっていたため、分けて整頓した。各担当者の金型探す手間の減少。
移動その1:加工用材料を材料置き場からクレーンを用いて台車に乗せ、運搬する。→ある特定の製品の材料を材料置き場で台車に取り分けて運搬するが都度クレーンを使うと工数がかさむので各部品用材料ごとに平置き。→別案件対応の為、材料置き場レイアウト変更。スペースも限られるため平置き案は止め、元に戻した。
移動その2:今まで…必要な金型を都度置いてあるところまで取りに行った。改善後…専用移動台車を設け、必要な金型をまとめて台車に乗せて複合機まで戻るようにした。移動回数・距離を削減した。
直接工数削減において、実施した改善。(複合機での加工部品・板厚問わず、共通する項目)
②-a.1回のパンチ加工を行う速度(以下プレス速度)を本機械で出せる限界まで上げた。
②-a.1回のパンチ加工から次のパンチ加工のため、材料を移動させる速度(以下「早送り選択」)を5段階中2段階目に早い速度に設定した。(最高速は材料クランプが外れる恐れある為、常用していない。)共通項目ではないが、板厚・個別プログラム単位にて実施した改善。
②-b.板厚毎:レーザー加工時のレーザーヘッドの移動速度(以下レーザー制御)を標準から1段階上げて早めた。(3段階中、2番目に早い速度。最高速はメーカー非推奨につき実施せず。)
②-b.個別:レーザー加工プログラムの大元(設計側PCでのみ変更可能な項目)にて、レーザー加工を早める設定(以下高速設定)を行った。新規発行分は全て実施してもらうよう設計側に伝達済み。(大幅な改善ではないが多少早まった。)
②-b.個別:レーザーパラメータを調整し、品質を担保できる範囲で速度を上げた。
具体的な数値はこの場で示すことはできませんが品物によっては2割~3割加工工数を減らすことができました。
また金型配置環境改善により、作業者同士の金型の取り合い削減・金型段取り工数削減につながりました。(金型を多く使う製品ほど効果が大きい)結果として今までの加工工数(複合機のプログラムに表示してある理論値の工数)よりも早く加工が済み、稼働率は下がります。
その分、日によってはフリーの時間が幾らか出来ます。複合機が関係する案件の受注残と納期を考慮しながら、可能な範囲で負荷率の高い他工程の手伝い・支援を職長と相談し、行いました。
目先の生産性向上はアップしますが中長期では他に考える必要があると感じます。
今後も都度メンバーと相談しながら生産性向上について考え出来ることから実行したいと思います。
以上